Engineer Awarded Grant to Study Metal Powder Behavior in 3-D Printing
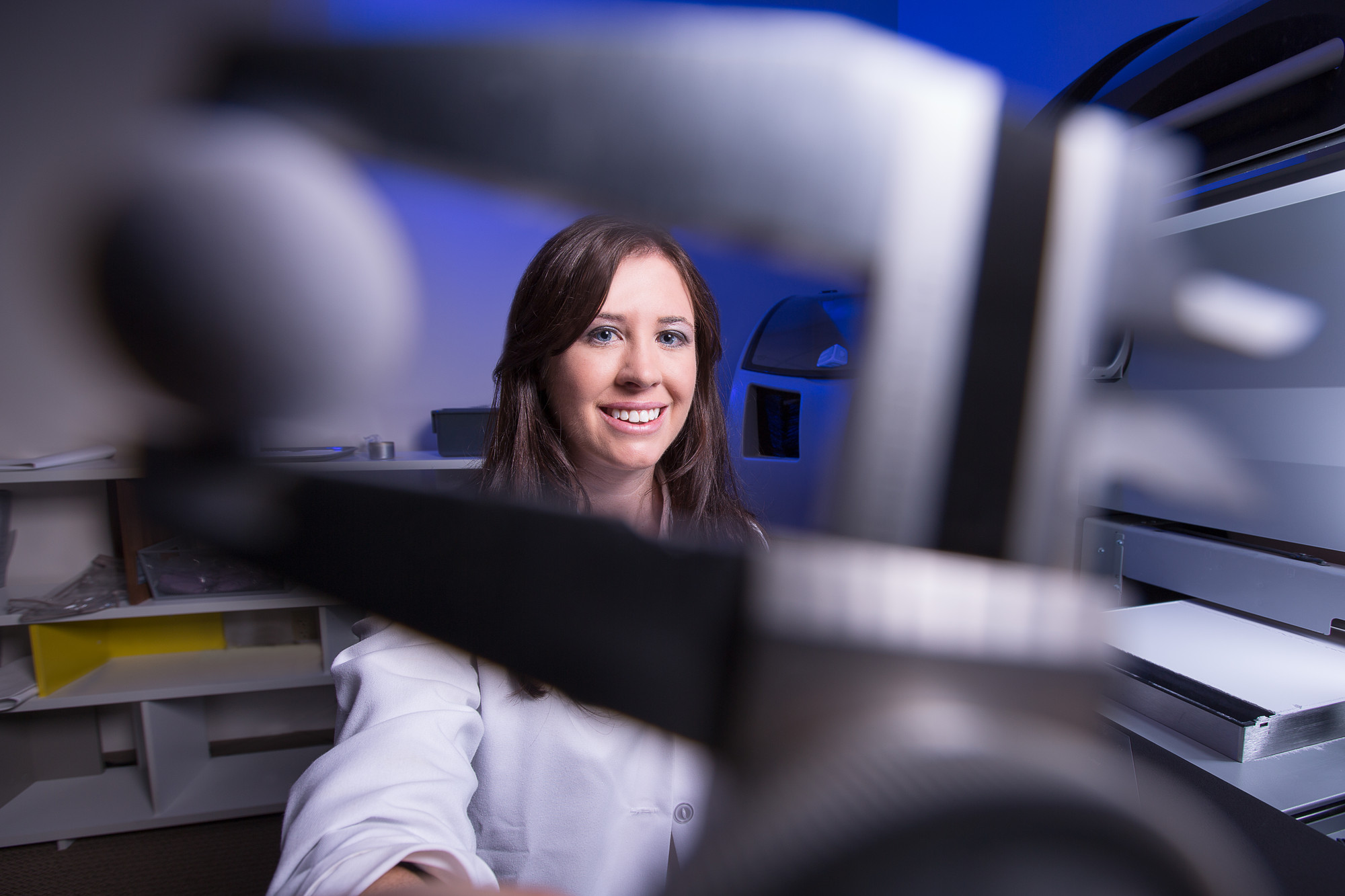
Michelle Bernhardt, assistant professor of civil engineering. Photo by Matt Reynolds, University of Arkansas
FAYETTEVILLE, Ark. – As a geotechnical engineer, Michelle Bernhardt is intrigued by the behavior and properties of granular materials such as sand.
“Granular materials behave similarly no matter what type of granular material they are,” said Bernhardt, an assistant professor of civil engineering in the College of Engineering at the University of Arkansas. “There are certain characteristics of their behaviors, however, which depend on the types of material and their shapes.”
Bernhardt uses computer modeling to break down materials into smaller parts. Using a method called discrete element method modeling, Bernhardt digitally simulates particles to study how they react to displacements and stress, such as those caused by an earthquake. She validates her simulations in the lab using small objects such as ball bearings.
Bernhardt’s discrete element method modeling simulation process drew the attention of the National Institute of Standards and Technology, a technology agency within the U.S. Department of Commerce, which in September awarded Bernhardt a three-year grant for $340,035.
Bernhardt’s research is highlighted in the October 2014 issue of The Arkansas Catalyst, an online monthly newsletter from the Office of Research and Economic Development.
In her project, Bernhardt will develop discrete element method simulations that can be used to examine the metal powder behavior in direct metal laser sintering devices, one of the techniques known as additive manufacturing.
“Additive manufacturing processes build a 3-D object such as a metal part layer by layer,” Bernhardt said. “This particular type of printer spreads a layer of metal powder across a build surface and a laser sinters the metal layer by layer, creating a 3-D object. Discrete element modeling captures the movements and interactions of each powder particle. The National Institute of Standards and Technology is interested in finding out how the powder particles are distributed when the printer arm moves the powder across the build surface, and whether that is going to change the properties of the material that is actually made.”
The simulations will be used to examine the initial packing of the powder, as well as the density and size distribution across the build surface with and without a 3-D object present, Bernhardt said. Each of these factors affects the quality of the built part and understanding how the powder is distributed on the build surface will help link the build conditions with the characteristics observed in the final product. From a manufacturing standpoint, this information will also help increase the quality control of various build conditions, she said.
“There are a lot of aerospace and other applications where you want to make sure the printed part is going to behave like you expect and that the engineering properties are the same each time it is printed,” she said.
Contacts
Michelle Bernhardt, assistant professor
Civil Engineering
479-575-6027, mlbernha@uark.edu
Chris Branam, research communications writer/editor
University Relations
479-575-4737,
cwbranam@uark.edu