Electric Car Battery Charger Prototype Aims for More Efficiency and Power
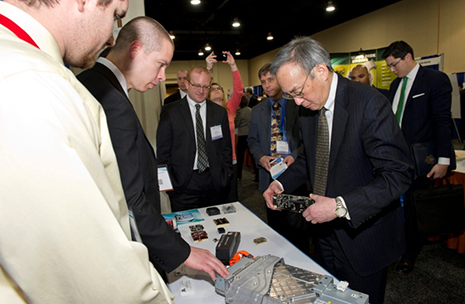
U.S. Secretary of Energy Steven Chu looks at the prototype of the silicon-carbide battery at the 2013 Energy Innovation Summit in Washington D.C.
FAYETTEVILLE, Ark. – Arkansas Power Electronics International Inc., a Genesis Technology Incubator client at the University of Arkansas, has developed a prototype battery charger for Toyota’s plug-in hybrid electric vehicle battery charger. The charger is designed to be more efficient, more powerful and smaller.
The company, located at the Arkansas Research and Technology Park in Fayetteville, is testing the device with a Toyota Prius, said Ty McNutt, director of business development at Arkansas Power Electronics International (APEI). The on-board charger converts alternating current power to controllable direct current power in order to charge the vehicle’s battery bank.
“We’ve demonstrated the silicon-carbide-based battery charger on the laboratory bench and are currently integrating it into a Prius vehicle,” McNutt said. “Over the next three months we’ll be doing significant testing in the vehicle, including charging the battery bank to look for efficiency, the speed-of-charge and how it interfaces with the existing battery management system.”
It will likely be at least five years before the battery charger is ready to go into a production vehicle line, McNutt said. But so far, the results are promising.
“At the core of the charger unit is a power module and our high-speed switching capability and high-temperature packaging capability allowed us to create a battery charger that is more efficient and more powerful,” McNutt said. “We’ve been able to get a product that is 10 times smaller and lighter weight than existing silicon-based chargers. We can also produce almost three times the amount of through power with the charger, at an increased efficiency. ”
APEI focuses on technology that makes things smaller — such as power modules used in vehicles, geological exploration and the aerospace industry. To shrink the size of such devices, company scientists have focused on silicon carbide, which can operate at temperatures up to 1,112 degrees Fahrenheit.
Graduate students at the U of A, under the direction of Alan Mantooth, Distinguished Professor of electrical engineering, are working on the integrated circuit, which will be the control chip for the power switch in the charger.
“The power switch turns on and off to transform from the alternating current coming out of the wall into the direct current that charges the batteries,” McNutt said. “To do it efficiently that power switch needs to be very fast, so that control chip also needs to be very fast.”
If the tests are successful, APEI is investigating ways to mass-produce the battery charger either at its manufacturing facility at the technology park or with the company’s manufacturing partners, McNutt said. It could license the technology to Toyota, he said.
APEI has been working on the battery charger for the last two and a half years in a collaborative research partnership that includes four other entities — the National Center for Reliable Electric Power Transmission, an academic research center based at the University of Arkansas; Oak Ridge National Laboratory; Cree Inc.; and Toyota Motor Engineering & Manufacturing North America Inc.
The U.S. Department of Energy, through its Advanced Research Projects Agency-Energy (ARPA-E), funded the project with a $3.9 million award in the fall of 2010. Arkansas Power Electronics International, the overall leader of the effort, is a private partner of the National Center for Reliable Electric Power Transmission.
Toyota is providing the Prius as well as technical support and specifications and the National Center for Reliable Electric Power Transmission and Oak Ridge National Laboratory are designing integrated circuits on semiconductor chips provided by Cree.
U.S. Secretary of Energy Steven Chu discussed the battery charger with McNutt at the 2013 Energy Innovation Summit, held in Washington D.C., in February. APEI was the only company from Arkansas with a booth at the summit’s technology showcase, which displayed more than 240 energy technologies.
APEI has about 40 employees. The company is likely to grow if the power module is manufactured in its manufacturing facility, McNutt said.
Contacts
Ty McNutt, director of business development
Arkansas Power Electronics International Inc.
479-575-5759, tmcnutt@apei.net
Chris Branam, research communications writer/editor
University Relations
479-575-4737,
cwbranam@uark.edu