University Center Trains Transportation Professionals
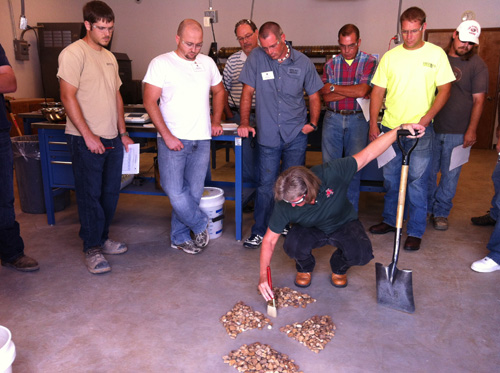
CTTP instructor Mary Fleck demonstrates one method of dividing an aggregate sample for testing.
In a civil engineering laboratory at the University of Arkansas Engineering Research Center, several groups of men and women stand around piles of rock and gravel. Their assignment is to separate these piles into smaller piles for analysis, but there’s a catch. Each smaller pile must be a representative sample of the larger pile; it must contain the same proportion of rock, gravel, sand and dirt as the original pile. In order to do this, they mix the rocks thoroughly and carefully divide the original pile into four parts, using a broom to keep every piece of sand and dust in the correct pile. Then, they discard two of the piles and mix the remaining two together. Finally, they weigh the sample. If it is still too large to be tested, they will repeat the process.
These are not college students; they are highway department employees and contractors whose jobs will involve quality control testing on the state’s highway construction projects. In order to ensure that our roads are safe and sturdy, highway department officials and contractors conduct many different types of tests. Aggregate — the gravel or crushed stone that provides structure to concrete and asphalt — must be tested to make sure is has the proper gradation and density for each project. Officials must also test the strength and other qualities of concrete and asphalt, and they perform tests on the soil under roadways.
The two and a half day course these students are taking is over aggregates. After they get the right sample size, they will learn how to use special sieves to separate the sample into course and fine material so they can make sure the aggregate contains the right proportion of each.
In 1996, a new federal regulation required that states use “qualified sampling and testing personnel” for projects involving federal money. In most states, the local transportation department trains its own employees and contractors to perform this testing, but in Arkansas, the University of Arkansas Center for Training Transportation Professionals performs all of this training and certification, providing the state with the security of having a third-party certifying these important professionals. The center trains around 400 or 500 students a year.
In addition to certifying these employees, the Center for Training Transportation Professionals also provides laboratory certification, visiting labs where the testing is conducted to make sure all the equipment and procedures are correct.
Stacy Williams, director of the center, explained why certification is so important. “Part of the issue of quality is consistency,” she said. “There are test methods out there, but people don’t always do it right. Variations get passed down.” At the Center for Training Transportation Professionals, all inspectors, engineers and contractors receive the same training and take the same tests.
Ralph Hall, who was the assistant chief engineer for operations at the Arkansas Highway and Transportation Department in 1996, recalls that involving the University of Arkansas in this project was an obvious choice. Dan Flowers, the director of the department at the time, was already working closely with civil engineering professors Walter LeFevre and Kevin Hall through the Mack Blackwell Transportation Center. “Dr. Hall was very interested and instrumental in showing us what the university could do,” said Ralph Hall, who is now the assistant to the AHTD director. “It seemed to all fit together right at the time.”
Having this training and testing associated with a university has several additional benefits. Civil engineering students can serve as test proctors, which gives them hands-on experience as well as opportunities to network with highway department professionals and transportation contractors. This provides an important link between the University of Arkansas civil engineering department and the industry that it serves.
Another benefit is the effect this link has on research. Williams, whose research involves developing standards for the testing of new asphalt materials, finds the contacts she makes through the Center for Training Transportation Professionals program to be invaluable. “We’re part of the community,” she said.
Working closely with the training center and transportation department staff, who are also responsible for inspecting and “spot checking” contractors’ labs, can also give the contractors a new perspective on inspections and bridge the gap between these groups.
“They can ask their inspectors questions,” Williams explained. “And when people challenge the inspection protocol, they can explain the reasons why these specifications are in place.”
As director of the training center, Williams has seen a lot of changes. Lately, she has noticed more new contractors coming in for certification, which she sees as a sign that the economic downturn, which caused a decrease in enrollment several years ago, is easing. She also noticed that with the downturn, small businesses began selling out to larger companies, making the industry more consolidated.
The training center is changing, as well. Recently, it developed online modules that give students an opportunity to get a head start on skills before the classes begin. In addition, an online refresher for the aggregates class, which doesn’t require any re-certification, ensures that inspectors and contractors stay up to date on the latest information.
Contacts
Camilla Medders, director of communications
College of Engineering
479-575-5697, camillam@uark.edu