'Fabcraft' Exhibit Showcases Computational Design and Fabrication Methods
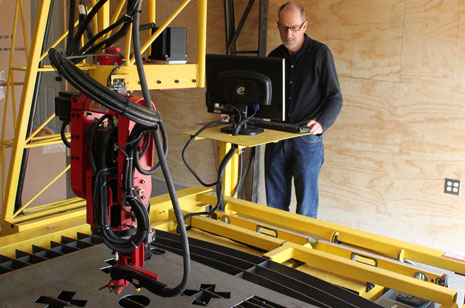
Santiago R. Perez, assistant professor of architecture, operates the computer on this custom-made machine that does computer numerically controlled plasma cutting and five-axis milling.
FAYETTEVILLE, Ark. – Santiago R. Perez has organized the “Fabcraft” exhibit, which will include some of his students’ projects from the fall semester, as well as pieces created during workshops in February. The exhibit pieces, created through computational design and fabrication methods, will be on display from March 3 through April 17 at the University of Arkansas Student Gallery – known as sUgAR – in downtown Bentonville. A reception is planned from 5:30 to 7:30 p.m., Friday March 4.
The name “Fabcraft” connotes an effort to explore and promulgate the value that digital fabrication technologies might have for the built environment. In the past, digital fabrication initiatives have involved creating complicated forms without a sense of directed purpose, simply “geometric experimentation,” said Perez, an assistant professor of architecture who holds the 21st Century Chair in Integrated Practice at the Fay Jones School of Architecture at the university.
“Fabcraft brings together advanced fabrication and more traditional craft-based methods and practices,” Perez said. These methods and practices gather people in fields as diverse as craft, design, math and robotics.
The sUgAR gallery showcases the work of students, faculty and visiting artists in the disciplines of architecture, landscape architecture, interior design and art. The gallery, located at 114 W. Central Ave. in Bentonville, is open from 2 to 6 p.m. Thursdays, from 10 a.m. to 5 p.m. Fridays and Saturdays, and from 1 to 5 p.m. Sundays.
Pieces on display for “Fabcraft” will include concrete work by Ryan Campbell and a cantilever structure created by team members Blake Leonard, James Rhoe and Brandon Bissram.
Campbell used the school’s three-axis mill to produce complex geometries in foam that could then be used as molds for casting concrete. Campbell worked with Eugene Sargent, a local artist and craftsman, as they added the fiber basalt to strengthen the concrete when they cast it at Sargent’s studio.
“They made an innovative, high-strength concrete mix that they then utilized to cast these complex geometries,” Perez said. Campbell also created concrete pieces from flexible fabric forms.
For the cantilever project last semester, Perez brought advanced design software into the third-year studio so students could generate complex patterns and geometry. Once students developed their patterns conceptually, they then had to physically cut the shapes from wood, connect them and load test the resulting pieces in cantilever fashion.
“The cantilever was an attempt at bringing a cellular logic, in which you connect many components together and they gain strength by virtue of their connections,” Perez said. “It involved structural performance and complex geometric patterning that was derived computationally.” Jerry Wall, professor of architecture, assisted students with structural concepts and evaluation of their work.
The exhibiting team used common household twine to connect their cantilever piece. They were “looking at how to increase the strength of materials that would normally be thought of as low strength materials by combining the elasticity or flexibility of the twine with the rigidity of the wood pieces they were connecting,” Perez said.
Building strength from a combination of materials is a technique that has been used by Japanese architect Shigeru Ban, whose work Perez wrote about in the introduction to the book Outside the Box: Cardboard Design Now.
Additional exhibited pieces will result from work produced during the Celento/Perez Steelcraft and Parametric Craft workshops in February. Collectively, these workshops in Fayetteville and the culminating exhibit in Bentonville serve to inaugurate the opening of the school’s new Advance Digital Fabrication Lab in south Fayetteville.
The Celento/Perez Steelcraft workshop, held Feb. 17-19, featured collaborative work created using computer numerically controlled plasma cutting and five-axis milling. For this, Perez worked with David Celento, an assistant professor of architecture from Pennsylvania State University.
Studio Mode, the Brooklyn-based team of Ronnie Parsons and Gil Akos, will lead the Parametric Craft workshop Feb. 26-28 in Vol Walker Hall. This workshop will focus on digital form finding through the use of parametric software called Rhino Grasshopper, coupled with the debut of the new Kangaroo software. Kangaroo allows real-world, physics-based forces, like wind and gravity, to interact with a three-dimensional model. The Studio Mode partners and students will create pieces using polypropylene, a commonly recycled plastic.
Contacts
Santiago Perez, assistant professor, architecture
Fay Jones School of Architecture
479-575-4705, srperez@uark.edu
John Orr, student director
University of Arkansas Student Gallery
479-273-5305, nevado1997@yahoo.com
Michelle Parks, senior director of marketing and communications
Fay Jones School of Architecture and Design
479-575-4704,
mparks17@uark.edu